신발제조 공정에서 화학물질 사용을 크게 줄일 수 있는 갑피 원단이 개발됐다.
한국신발피혁연구원은 산업통상자원부 핵심부품소재 개발사업의 하나로 ‘프라이머 처리가 필요 없는 신발 갑피 원단’을 개발하는 데 성공했다고 4일 밝혔다.
신발 제조 공정은 갑피(Upper), 중창(Mid-sole), 겉창(Out-sole)으로 이뤄진다.
이 가운데 갑피는 신발 겉 재료 표면을 갈아내는 버핑(Buffing) 공정과 접착이 잘되도록 돕는 프라이머(일명 선처리제) 1차 도포 공정, 1차 건조 공정, 접착제 2차 도포 공정, 2차 건조 공정 등 모두 5단계 공정으로 조립한다.
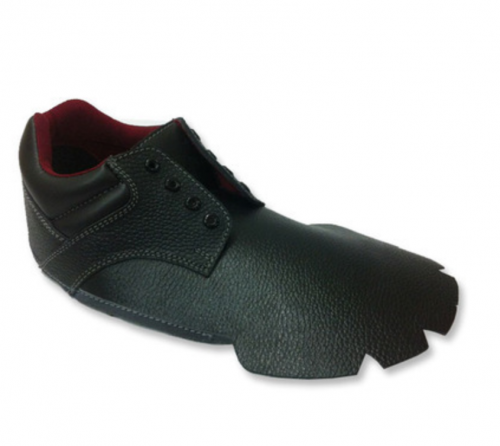
갑피 조립 공정은 과정이 복잡하고 시간이 많이 들어 신발산업 경쟁력을 결정하는 주요 공정으로 알려졌다.
특히 버핑 과정에서 발생하는 분진과 선처리제 도포 과정에 사용하는 휘발성 유기화합물은 작업 환경을 오염시키고 작업자 건강을 위협하는 원인으로 지목됐다.
한국신발피혁연구원이 개발한 갑피 원단은 버핑 공정과 프라이머 처리 공정을 생략하고 접착제 도포와 건조 공정만으로 갑피 조립이 가능하다.
기존 5단계 공정을 2단계로 줄이면서 60%가량 공정 간소화를 이뤄 신발 제조 원가 절감과 경쟁력 향상에 크게 기여할 것으로 기대된다.
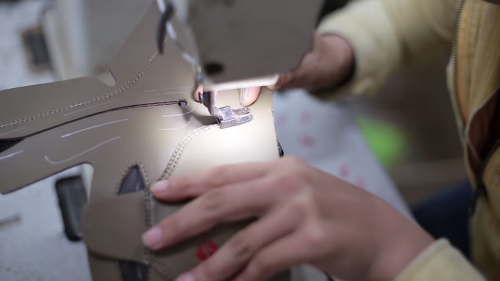
백인규 한국신발피혁연구원 그린화학연구실장은 “새로 개발한 갑피 원단을 사용하면 화학물질로부터 작업자 건강을 지키고 작업환경을 개선할 수 있다”며 “전체 신발제조 공정을 단축해 원가를 절감하고 생산 자동화에도 강점을 지닌다”고 말했다.
이번에 개발한 갑피 소재는 부산에 본사를 둔 스포츠용품 제조업체 학산에서 하반기부터 신발 완제품 생산에 사용할 계획이다.
연합뉴스